Tiết kiệm gần 1 tỷ đồng từ việc sử dụng năng lượng hợp lý
Thứ bảy, 11/02/2012 - 14:52
Các giải pháp Công ty đã thực hiện có hiệu quả sử dụng năng lượng cao, tiết kiệm trên 30,3% chi phí so với ban đầu.
Nằm trên địa bàn tỉnh Hải Dương, Công ty TNHH Hồng Dương là doanh nghiệp chuyên sản xuất chế biến các sản phẩm nông sản, thực phẩm, muối các loại với năng lực sản xuất đạt tới 12.000 tấn muối/năm. Mặc dù được đầu tư trang thiết bị tương đối đồng bộ, hiện đại, nhưng hàng năm, Công ty vẫn tiêu thụ lượng điện năng khá lớn. Đây chính là vấn đề khiến cho Ban Lãnh đạo Công ty trăn trở, làm thế nào để giảm được các nguồn tiêu hao này.
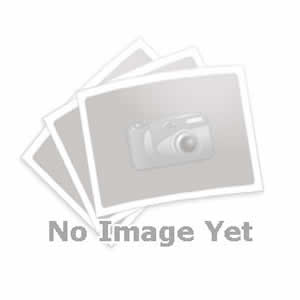
Xuất phát từ nhu cầu thực tế, đồng thời nhằm góp phần tích cực vào việc thực hiện thành công Đề án “Sử dụng năng lượng tiết kiệm và hiệu quả trên địa bàn tỉnh Hải Dương giai đoạn 2009-2013, Công ty Hồng Dương đã triển khai nhiều biện pháp thực hiện tiết kiệm năng lượng tại doanh nghiệp. Theo đánh giá của Trung tâm nghiên cứu Khoa học và Công nghệ (Sở KH&CN) Hải Dương thì Công ty TNHH Hồng Dương là một trong những doanh nghiệp tiêu biểu của tỉnh Hải Dương trong việc kiểm toán năng lượng cũng như thực hiện các giải pháp tiết kiệm năng lượng.
Công nghệ sản xuất của Công ty gồm khá nhiều các công đoạn khác nhau và có những yêu cầu nghiêm ngặt về vệ sinh an toàn cũng như các yêu cầu khác của quá trình sản xuất các sản phẩm. Nguyên liệu chính của Công ty là muối nguyên liệu được nhập khẩu chủ yếu từ Ấn Độ, nguyên liệu này được bảo quản trong kho chứa của Công ty. Tại đây diễn ra quá trình nghiền sơ bộ, những hạt muối có kích cỡ đủ nhỏ sẽ được bơm tiếp lên xyclon số 2 và được nghiền tinh tại máy nghiền cấp 2. Những hạt có kích cỡ lớn sẽ ở lại trên mặt sàng và tiếp tục được nghiền đến kích cỡ mong muốn. Muối sau khi đủ tiêu chuẩn về cỡ hạt sẽ được đẩy sang máy vắt nước. Máy vắt nước ly tâm có nhiệm vụ loại bỏ một phần nước trong muối. Muối sau khi được vắt trở thành muối tinh và được trộn i-ốt theo tỷ lệ tiêu chuẩn (đối với sản phẩm muối i-ốt) và chuyển sang công đoạn sấy tiếp theo. Muối thành phẩm được đóng bao và được trữ ở trong kho thành phẩm trước khi xuất xưởng.
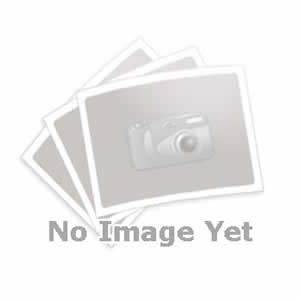
Sau khi kiểm toán cho thấy, tại khu vực sấy sử dụng than làm nhiên liệu, việc vận hành các lò than tương đối kém hiệu quả. Do sự không tương xứng giữa lưu lượng gió cấp và lượng than đưa vào nên quá trình cháy là chưa tối ưu. Do đó hiệu quả của quá trình đốt nhiên liệu là rất thấp. Bên cạnh đó, trong quá trình sản xuất, công đoạn sấy muối, nước trong muối được tách ra và phát sinh ra một lượng nhiệt và hơi nước đáng kể nên khu vực này tương đối nóng và ẩm. Đây cũng là khu vực mà Công ty rất quan tâm để cải thiện môi trường sản xuất cho công nhân.
Khảo sát sơ bộ tại hệ thống sấy muối cho thấy, thùng quay sấy muối đã cũ và tiêu hao nhiên liệu lớn, việc vận hành hệ thống sấy chủ yếu dựa vào lao động thủ công, dẫn đến môi trường sản xuất bị ảnh hưởng khá lớn. Mặt khác, do nhu cầu mở rộng sản xuất của Công ty nên đòi hỏi hệ thống sấy cần đầu tư thay thế để tăng công suất, nhưng tiêu hao ít nhiên liệu hơn, đồng thời phải giảm chi phí nhân công, tăng chất lượng sản phẩm.
Tại dây chuyền chế biến muối sử dụng 04 động cơ khuấy có công suất 15 kWh/động cơ. Những động cơ này có tốc độ vòng quay 950 vòng/phút, tuy nhiên, tốc độ khuấy chỉ là 300 vòng/phút, thời gian hoạt động khoảng 8 giờ/ngày. Từ thực tế đó, Công ty thay thế dây chuyền sấy muối cũ bằng dây chuyền mới, có công suất lớn hơn 2,5 lần công suất hiện tại, đồng thời tận dụng một phần nhiệt năng của khói thải trong dây chuyền mới để sấy nông sản. Dây chuyền mới sẽ được nối trực tiếp vào phía sau dây chuyền chế biến muối tinh. Cùng với đó, Công ty lắp đặt thiết bị biến tần để điều chỉnh tốc độ động cơ khuấy nguyên liệu nhằm giảm tiêu hao điện năng cho các động cơ này. Sau khi dây chuyền mới vào hoạt động, Trung tâm Ứng dụng tiến bộ khoa học được sự hỗ trợ kỹ thuật của Viện Nhiệt lạnh - Trường Đại học Bách khoa Hà Nội đã tiến hành khảo sát, đo đạc để tính toán mức tiết kiệm năng lượng thực tế đạt được. Kết quả cho thấy, việc lắp đặt dây chuyền mới tiết kiệm hơn 758,64 triệu đồng/năm. Đặc biệt, với dây chuyền sản xuất mới, chất lượng của sản phẩm cũng tăng lên, đảm bảo các yêu cầu về vệ sinh an toàn thực phẩm, tăng sức cạnh tranh trên thị trường trong và ngoài nước.
Đại diện lãnh đạo Công ty cho biết, các giải pháp Công ty đã thực hiện có hiệu quả sử dụng năng lượng cao, tiết kiệm trên 30,3% chi phí so với ban đầu. Việc lắp đặt dây chuyền mới hiện đại còn giúp cải thiện môi trường làm việc của người lao động, nâng cao chất lượng sản phẩm, mở ra cho doanh nghiệp cơ hội nâng cao năng suất, chất lượng, đáp ứng được nhu cầu của thị trường trong và ngoài nước.
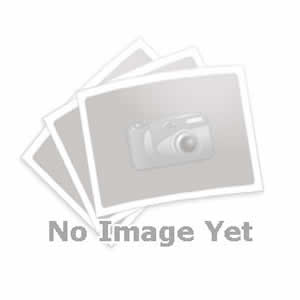
Xuất phát từ nhu cầu thực tế, đồng thời nhằm góp phần tích cực vào việc thực hiện thành công Đề án “Sử dụng năng lượng tiết kiệm và hiệu quả trên địa bàn tỉnh Hải Dương giai đoạn 2009-2013, Công ty Hồng Dương đã triển khai nhiều biện pháp thực hiện tiết kiệm năng lượng tại doanh nghiệp. Theo đánh giá của Trung tâm nghiên cứu Khoa học và Công nghệ (Sở KH&CN) Hải Dương thì Công ty TNHH Hồng Dương là một trong những doanh nghiệp tiêu biểu của tỉnh Hải Dương trong việc kiểm toán năng lượng cũng như thực hiện các giải pháp tiết kiệm năng lượng.
Công nghệ sản xuất của Công ty gồm khá nhiều các công đoạn khác nhau và có những yêu cầu nghiêm ngặt về vệ sinh an toàn cũng như các yêu cầu khác của quá trình sản xuất các sản phẩm. Nguyên liệu chính của Công ty là muối nguyên liệu được nhập khẩu chủ yếu từ Ấn Độ, nguyên liệu này được bảo quản trong kho chứa của Công ty. Tại đây diễn ra quá trình nghiền sơ bộ, những hạt muối có kích cỡ đủ nhỏ sẽ được bơm tiếp lên xyclon số 2 và được nghiền tinh tại máy nghiền cấp 2. Những hạt có kích cỡ lớn sẽ ở lại trên mặt sàng và tiếp tục được nghiền đến kích cỡ mong muốn. Muối sau khi đủ tiêu chuẩn về cỡ hạt sẽ được đẩy sang máy vắt nước. Máy vắt nước ly tâm có nhiệm vụ loại bỏ một phần nước trong muối. Muối sau khi được vắt trở thành muối tinh và được trộn i-ốt theo tỷ lệ tiêu chuẩn (đối với sản phẩm muối i-ốt) và chuyển sang công đoạn sấy tiếp theo. Muối thành phẩm được đóng bao và được trữ ở trong kho thành phẩm trước khi xuất xưởng.
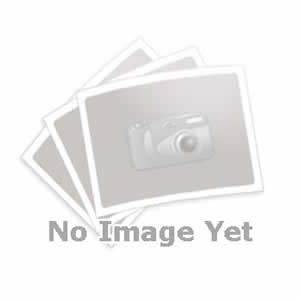
Sau khi kiểm toán cho thấy, tại khu vực sấy sử dụng than làm nhiên liệu, việc vận hành các lò than tương đối kém hiệu quả. Do sự không tương xứng giữa lưu lượng gió cấp và lượng than đưa vào nên quá trình cháy là chưa tối ưu. Do đó hiệu quả của quá trình đốt nhiên liệu là rất thấp. Bên cạnh đó, trong quá trình sản xuất, công đoạn sấy muối, nước trong muối được tách ra và phát sinh ra một lượng nhiệt và hơi nước đáng kể nên khu vực này tương đối nóng và ẩm. Đây cũng là khu vực mà Công ty rất quan tâm để cải thiện môi trường sản xuất cho công nhân.
Khảo sát sơ bộ tại hệ thống sấy muối cho thấy, thùng quay sấy muối đã cũ và tiêu hao nhiên liệu lớn, việc vận hành hệ thống sấy chủ yếu dựa vào lao động thủ công, dẫn đến môi trường sản xuất bị ảnh hưởng khá lớn. Mặt khác, do nhu cầu mở rộng sản xuất của Công ty nên đòi hỏi hệ thống sấy cần đầu tư thay thế để tăng công suất, nhưng tiêu hao ít nhiên liệu hơn, đồng thời phải giảm chi phí nhân công, tăng chất lượng sản phẩm.
Tại dây chuyền chế biến muối sử dụng 04 động cơ khuấy có công suất 15 kWh/động cơ. Những động cơ này có tốc độ vòng quay 950 vòng/phút, tuy nhiên, tốc độ khuấy chỉ là 300 vòng/phút, thời gian hoạt động khoảng 8 giờ/ngày. Từ thực tế đó, Công ty thay thế dây chuyền sấy muối cũ bằng dây chuyền mới, có công suất lớn hơn 2,5 lần công suất hiện tại, đồng thời tận dụng một phần nhiệt năng của khói thải trong dây chuyền mới để sấy nông sản. Dây chuyền mới sẽ được nối trực tiếp vào phía sau dây chuyền chế biến muối tinh. Cùng với đó, Công ty lắp đặt thiết bị biến tần để điều chỉnh tốc độ động cơ khuấy nguyên liệu nhằm giảm tiêu hao điện năng cho các động cơ này. Sau khi dây chuyền mới vào hoạt động, Trung tâm Ứng dụng tiến bộ khoa học được sự hỗ trợ kỹ thuật của Viện Nhiệt lạnh - Trường Đại học Bách khoa Hà Nội đã tiến hành khảo sát, đo đạc để tính toán mức tiết kiệm năng lượng thực tế đạt được. Kết quả cho thấy, việc lắp đặt dây chuyền mới tiết kiệm hơn 758,64 triệu đồng/năm. Đặc biệt, với dây chuyền sản xuất mới, chất lượng của sản phẩm cũng tăng lên, đảm bảo các yêu cầu về vệ sinh an toàn thực phẩm, tăng sức cạnh tranh trên thị trường trong và ngoài nước.
Đại diện lãnh đạo Công ty cho biết, các giải pháp Công ty đã thực hiện có hiệu quả sử dụng năng lượng cao, tiết kiệm trên 30,3% chi phí so với ban đầu. Việc lắp đặt dây chuyền mới hiện đại còn giúp cải thiện môi trường làm việc của người lao động, nâng cao chất lượng sản phẩm, mở ra cho doanh nghiệp cơ hội nâng cao năng suất, chất lượng, đáp ứng được nhu cầu của thị trường trong và ngoài nước.
Minh Sơn